Analysis and Modeling of Surface Roughness in Powder Mix EDM and Pure EDM Using Central Composite Design
DOI:
https://doi.org/10.37934/araset.30.1.243254Keywords:
Surface modification, Tantalum Carbide powder, EDM, central composite designAbstract
Conventional surface modification methods, such as ion insertion and laser surface melting, have recently seen growing importance in the innovative usage of the electrical discharge machining process (EDM) as a competitive substitute. Surface composition and properties are affected by several factors, including erosion of work materials and tool materials during the process, as well as the formation of plasma channels from the vaporized materials. This indicates that, under certain machining conditions, deliberate materials transfer may be possible using either a composite electrode by scattering metallic powders in a dielectric or a combination of the two. However, the traditional electrode has not been very successful in the surface modification process. Although it has been considered, expanding research into the use of powder additives through EDM techniques to enhance the level of surface modification is lacking. In addition, the pulse interval is not included in the existing works that examine the impact of technique parameters on surface modification. Because of this, a thorough optimization of the process has not been possible to characterize the connection between the independent variables under control and the machining parameters. To take full advantage of the benefits offered by EDM, it is necessary to learn more about the missing links between the process and its desired outcomes, such as whether or not surface alloying of metallic materials using EDM is feasible and what controls should be used for the various variables involved. The purpose of this study was to assess the efficiency of EDM-based surface alloying of stainless steel using Tantalum Carbide (TaC) powder as an additive by measuring the resulting surfaces' roughness (SR). It was found that RaPMEDM 11 recorded at current 5A and on-time 6.30 off-time 7.00 with powder concentration 25g/L. The RaPMEDM is easy to predict by controlling factor current (A) and on-time (B). At the higher current of 7.25A, RaPMEDM showed to decrease slightly. This result justifies TaC powder starts to control and modify the surface of stainless steel at a high factor current. In the case of without additives RaEDM, at maximum current 5 A, on-time 6.26 μs, and off-time 7 μs, RaEDM recorded 7 μm. Although it provided the highest Ra compared to RaPMEDM.
Downloads
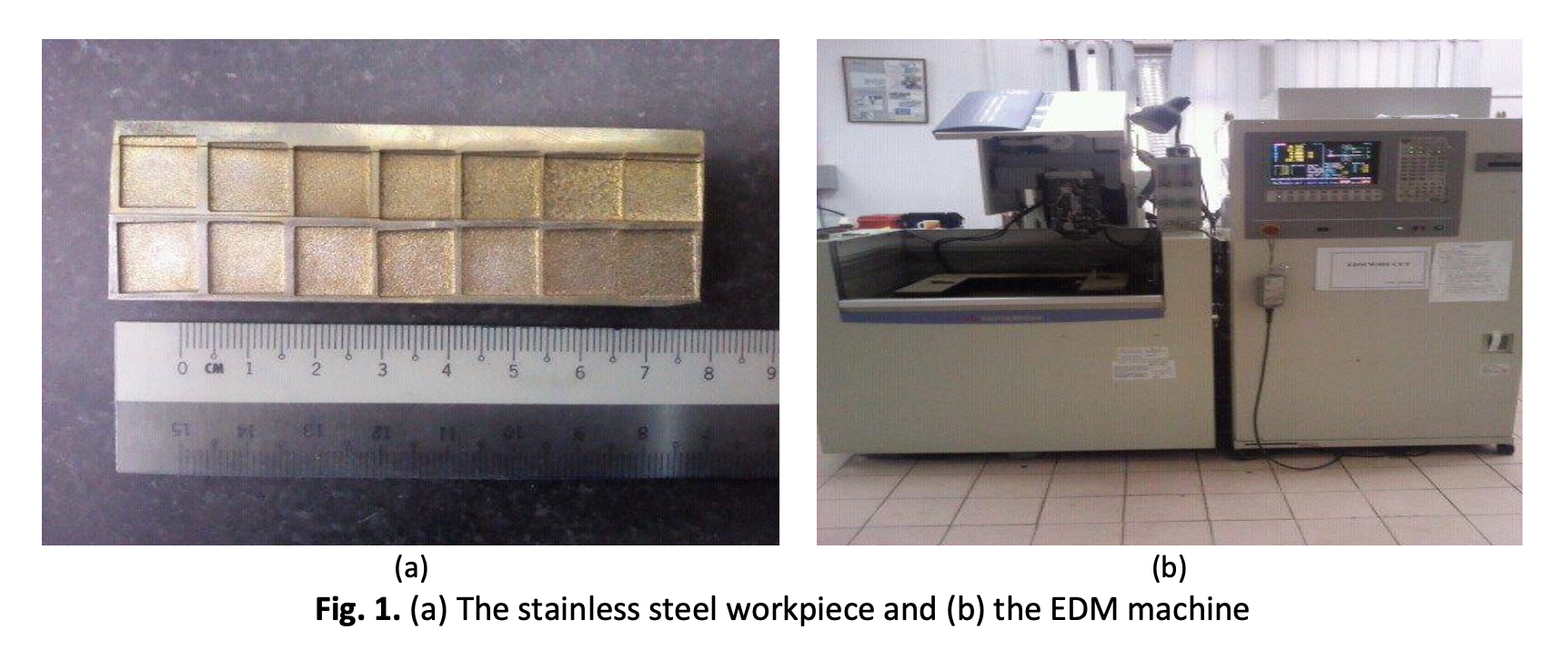