Best Practice of Striving Energy Sustainability in a Hot Press Machine for Clutch Facing Manufacture
DOI:
https://doi.org/10.37934/araset.30.2.6074Keywords:
Facing clutch, hot press machine, heat transfer oilAbstract
A facing clutch manufacturer in Surabaya, Indonesia, PT. X uses 20 hot press machines to produce the facings. The required heating process is provided by heat transfer oil (HTO), which is heated by natural gas burned in a heater. PT. X wants to reduce its natural gas consumption. The assessment started with checking the insulation on the piping system, measuring the temperature in the hot press machines, and measuring the HTO flow rate. The insulation in the piping system is in good condition. From the measurement, it was found that the HTO flow rate is adequate and fits the need of the heating process. Another finding is that the surface temperature of the lower plate in shaft no. 4 is the lowest than in the other shafts. The existing (asbestos) insulation from the lower bed in shaft no 4 to the hydraulic component is only 3 mm thick. This is not enough to prevent heat loss from the bed in shaft no. 4. The new 18-mm asbestos replaced the old asbestos. The replacement shows that the temperature at the mold surface at shaft no. 4 increased from 162.6°C to 170.9°C on average for MC-02 and from 166.7°C to 173.1°C on average for MC-03. Another achievement obtained is that the natural gas consumption was reduced by around 7.3% or 39 MMBtu/month, or equivalent to reducing 0.312 metric tons of CO2 per month. This is a simple effort to use less energy to protect our environment.
Downloads
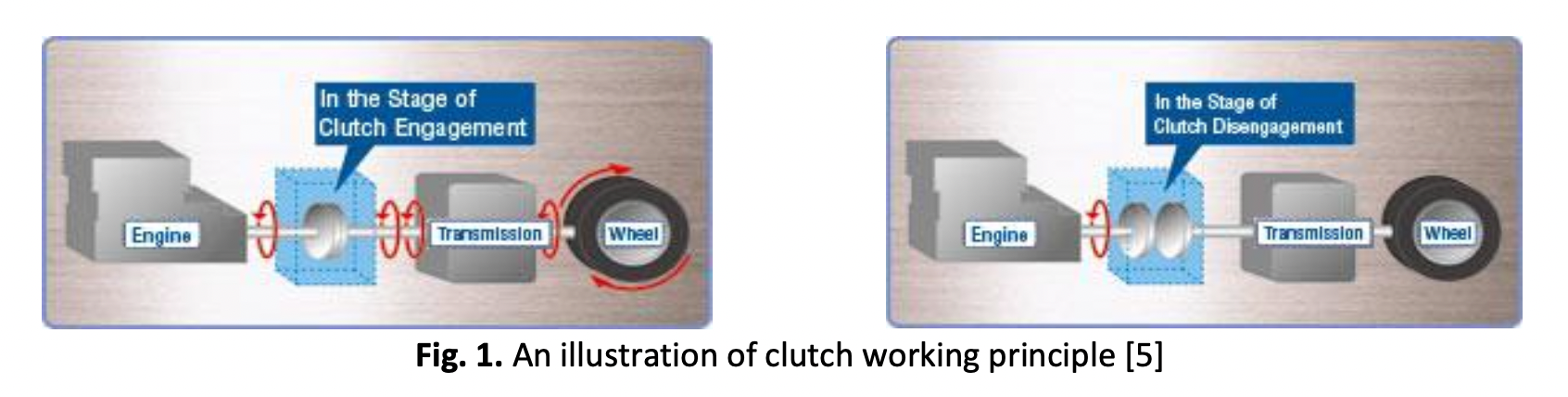