Failure Analysis of Valve Unit for MAN 9L21/31 Diesel Engine Generator
DOI:
https://doi.org/10.37934/araset.33.3.185193Keywords:
Microstructure, chemical composition, hardness test, diesel engine valve, power plantAbstract
Damage to the MAN 9L21/31 generator valve system caused issues with the industrial generator. The MAN 9L21/31 generator produces 1,980 kW and has nine in-line cylinders. It is powered by a gasoline engine. The purpose of this research was to harm the MAN 9L21/31 exhaust valve. The engine's cylinder head number 7 has a gutter that displays a temperature rise indication of up to 457 degrees Celsius. The procedure for analyzing valve hardness, chemical makeup, and microstructure. the outcomes of the material hardness test on Sample I-1 Numbers 10, 11, and 12 (523 HV), as well as on Sample I-2 Numbers 1 and 2 (558 HV) (523 HV). The valve face is hardened using electric arc welding using nickel, chromium, and high molybdenum alloy steel. According to microscopy testing, austenitic dendrites represent thermal fatigue corrosion in the region of the stellite microstructure. From the thick side, the microstructure of the bainite-ferrite valve base material can be seen, with fine carbide grains distributed evenly in several regions of thermal fatigue corrosion fracture. Austenitic dendrites, a type of thermal fatigue corrosion, also develop in the stellite microstructure region. More than 86.1%–86.5% Fe is the primary chemical component of the material that makes up the main valve. Hardness is produced by a carbon compound of iron with 0.038% to 0.042% carbon. Despite having a composition of only 1.67%, this Fe-C alloy is still referred to as alloy steel. It has excellent elastic and ductility properties thanks to the additional Si material, which ranges from 3.02% to 3.34%.
Downloads
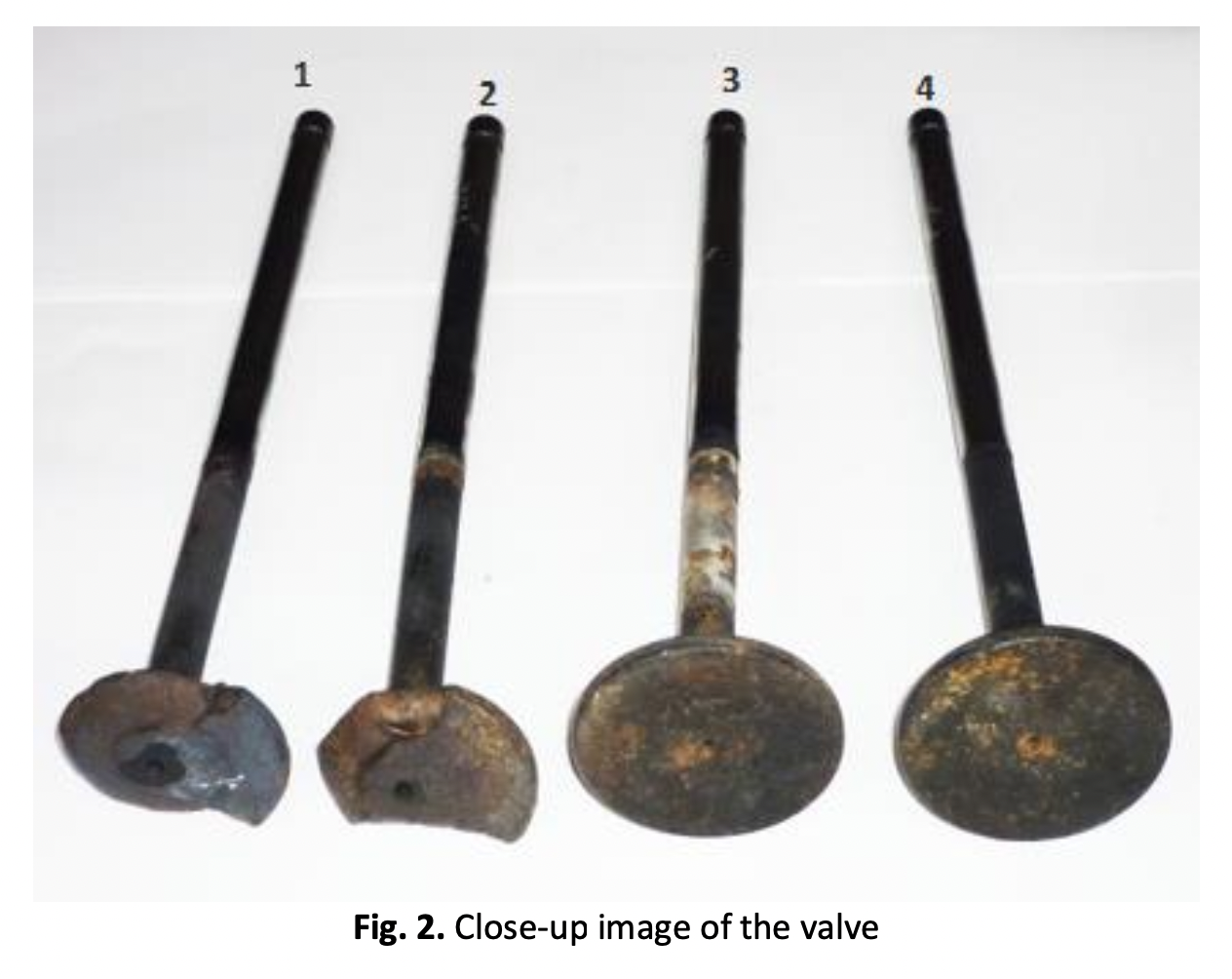