Impact Strain Signal Characteristics of Al and Mg under Instrumented Charpy Test
DOI:
https://doi.org/10.37934/araset.42.2.1326Keywords:
Charpy impact, Energy absorption, PSD energy, Impact duration, Impact strain signalAbstract
Impact strain signal is used to examine strain signal patterns under various parameters. Impact is a complicated phenomenon that occurs within a millisecond timeframe. Material toughness is measured by the energy absorption recorded by the Charpy machine and closely related to the specimen fracture deformation. By utilizing the strain gauge and data acquisition, the impact strain signal provides additional data regarding impact duration, maximum strain value and the area under curve for a deeper understanding of the impact problem. A material with high toughness has great energy absorption and the capability to withstand high impact load. Although magnesium is lighter in weight compared to aluminium, aluminium is a better corrosion-resistant material and is stronger, which makes it more suitable to be fabricated as automotive structural components. Tensile test is typically used for investigating a material’s mechanical properties. In the automotive industry, materials are required to have good crashworthiness. This study investigates the relationship between the energy absorbed with the power spectral density and the area under strain–time graph for different materials, impact speeds, and material thicknesses. Furthermore, the relationship between the stress–strain curve and impact strain signal were examined. In this study, the behaviour of two materials, namely Aluminium 6061-T6 and Magnesium AM60, was investigated using instrumented Charpy test, by referring to the impact strain signal pattern result. For the experiment, strain gauge attached to the Charpy machine striker was employed and linked to the data acquisition system. Charpy impact specimen has three different thicknesses; 10 mm, 7.5 mm and 5 mm. Impact speed is at 3.35 m/s and 5.18 m/s. Results show a correlation between energy absorbed with strain energy. Strain energy obtained is directly proportional to the energy absorbed. Aluminium 6061-T6 has the highest energy absorption, maximum strain, and strain energy under power spectral density graph compared to Magnesium AM60. Relation of strain signal from Charpy test and stress–strain curve from tensile test shows a significant finding where the material deforms and fracture points are identified through the signal pattern and curve. Thus, the strain signal pattern can be used to predict material behaviour.
Downloads
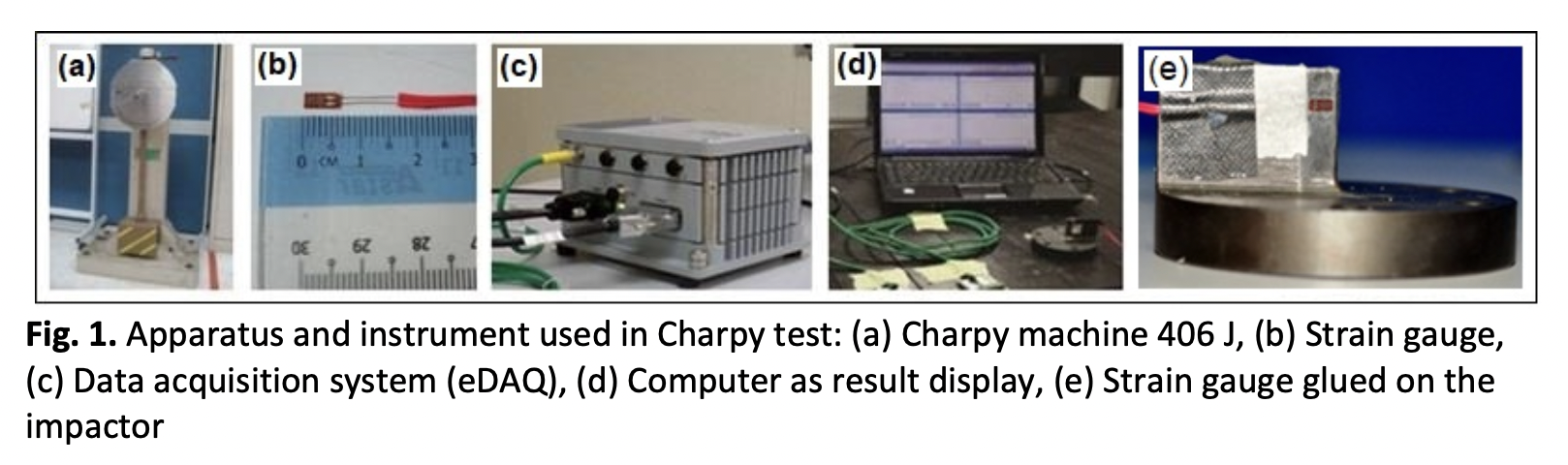