Computational Fluid Dynamic Analysis on Carbon Fibre Reinforced Polymer Wrapped on Defected Oil and Gas Piping System Using Solidwork Flow Simulation
DOI:
https://doi.org/10.37934/arfmts.101.2.197210Keywords:
Carbon Fiber Reinforced Polymer (CFRP), wrapping structure, Solidwork, Computational Fluid Dynamics (CFD), leakagesAbstract
Utilising Carbon Fibre Reinforced Polymer (CFRP) as a wrapping structure on defected piping system is not a very new approach in maintaining the defected pipe structure. But simulating the entire approach using computational simulation technique makes this research to be unique. This composite material was regarded as a one-of-a-kind wrapping material since it might have the combined properties of the element or significantly different properties than the constituents individually. Computational Fluid Dynamic (CFD) analysis is needed to make sure that the proposed wrapping structure doesn’t disrupt the fluid flow after the repair is done. The research is keen to fully utilise Solidwork flow simulation in evaluating the capability of proposed CFRP wrapping structure without any leaks or opening. Based on simulated data, this technique provides a preliminary analysis and visual deformations in selecting the suitable optimised lamination orientation of CFRP in real-world applications. Furthermore, the flow simulation study in SolidWorks has identified areas where possible fluid accumulation could occur after the repair has been done. This approach may prevent two primary failure modes by achieving the right lamination orientation and thickness which is CFRP overloading due to excessive thickness and CFRP delamination of the composite laminate from the substrate.
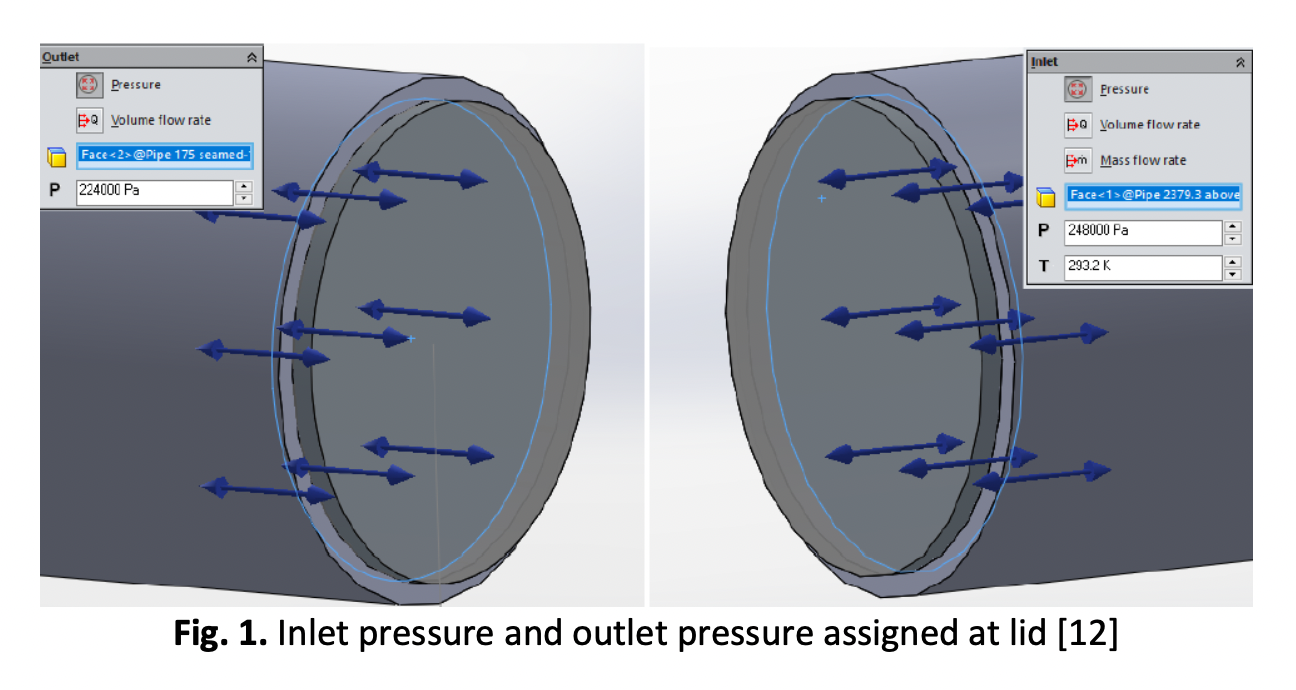