Optimization of Nozzle Design for Weight Reduction using Variable Wall Thickness
DOI:
https://doi.org/10.37934/arfmts.112.2.86101Keywords:
NPR, Mach number, factor of safety, CFD analysis, static structural analysisAbstract
In various fields, including rockets, turbines, and engines, the critical role played by nozzles in achieving optimal performance is underscored. Within the domain of rocketry, particular attention is given to the weight of the nozzle, where even the slightest modifications in weight can lead to a profound impact on rocket performance. In this research, an endeavor is made to comprehensively investigate the intricate interplay of nozzle pressure ratio, nozzle thickness, and Mach number, to unveil the effects of these parameters on nozzle deformation, the development of equivalent stress, and the pivotal factor of safety. Material optimization strategies for a wide array of flow and geometrical parameters are also explored within the framework of this study. With each parameter considered at four levels, an exploration is conducted across Mach numbers of 1.5, 2.0, 2.5, and 3.0, alongside Nozzle Pressure Ratios of 2, 4, 6, and 8. The meticulous analysis of nozzle thicknesses at levels of 1 mm, 2 mm, 3 mm, and 4 mm is carried out. The computational fluid dynamics (CFD) analysis is systematically executed across all cases, with resultant pressure profiles on the internal surfaces of the nozzle serving as essential boundary conditions for static structural analysis. The presentation of findings entails a comprehensive discussion of the factor of safety values for all parameter combinations. Significantly, it is observed from our results that a direct correlation exists between nozzle thickness and factor of safety, with an increase in nozzle thickness corresponding to an enhancement in factor of safety.
Downloads
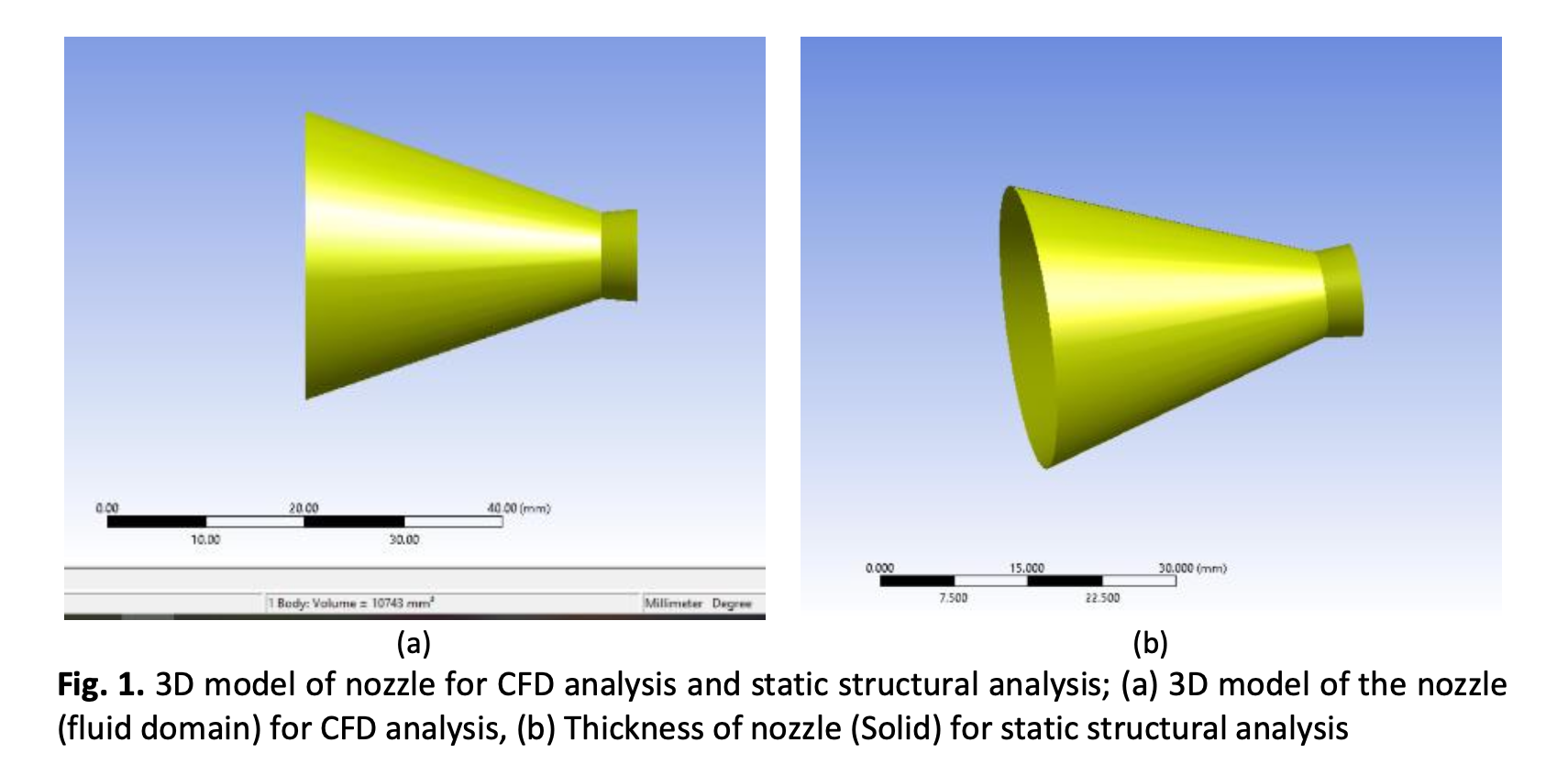