Hydrodynamic Load Effect on Composite Polymer Cold-Water Pipe Joint in Ocean Thermal Energy Conversion
DOI:
https://doi.org/10.37934/arfmts.113.1.141152Keywords:
Sea current, Thickness, Stress, Pipe, JointAbstract
The cold-water pipe in Ocean Thermal Energy Conversion (OTEC) is a very important part of the process of producing electrical energy. The cold-water pipe functions to convey cold water with a temperature of 5°C from a sea depth of >500 m to the sea surface. The cold water in the pipe is allowed to experience a temperature increase of <3°C so that it can be used to dilute the ammonia in the condenser. The use of polymer composites as cold-water pipe materials is a challenge because the hydrodynamic load from seawater currents fluctuates in a direction perpendicular to the position of the pipe. The pipe length reaches >500 m consisting of several pipes connected using the Friction Stir Welding method. This research was conducted to determine the effect of the hydrodynamic load of seawater currents on Friction Stir Welding (FSW) connections, the stress distribution in pipe joints, and the thickness of pipes that are safe to use as OTEC cold water pipes. In addition, simulations were carried out using Inventor software on pipes with a length of 500 m, a diameter of 4 m, and variations in thickness from 18 cm to 30 cm which produced von Mises yield stress and stress distribution at different joints at each pipe thickness. In pipes with a thickness of less than 20 cm, the stress and stress distribution are purely influenced by the hydrodynamic load of seawater currents. Meanwhile, in pipes with a thickness greater than 24 cm, the stress that occurs in the pipe is influenced by the current and weight of the pipe. In pipes with a thickness greater than 24 cm, the stress in the pipe is concentrated in the middle of the joint which is the critical part of the pipe and is the initial point of failure. It was found that at a pipe thickness of 22 cm, the stress was distributed almost evenly because the stress caused by seawater currents was reduced by the heavy load of the pipe. So, from the simulation of cold-water pipes with polymer composite materials that experience hydrodynamic loads from seawater currents varying in thickness from 16 cm to 30 cm, it is recommended to use a pipe thickness of 22 cm so that the pipe connection is safer as an ocean-based OTEC cold water pipe application.
Downloads
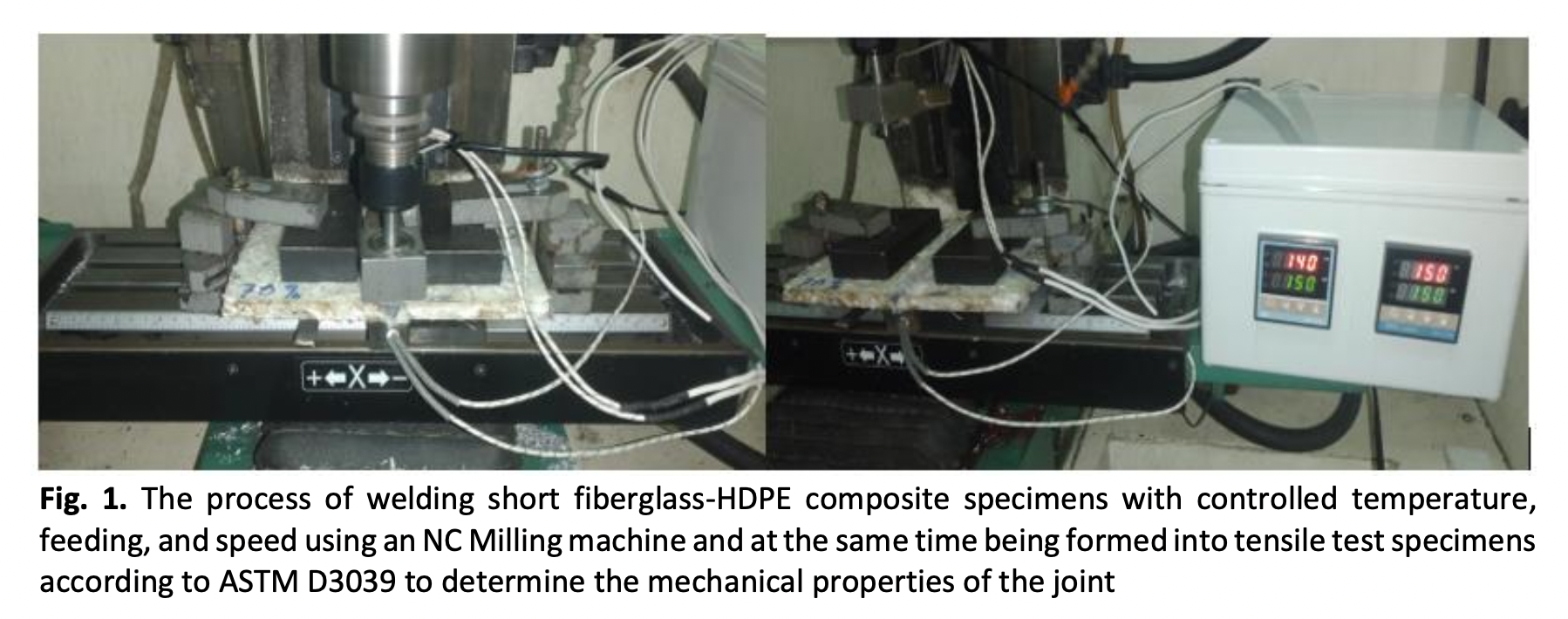