A Review of the Parameters Related to the Rubber Sheets Production: Major Constituents of Rubber Latex, Rubber Particles, Particle Interaction of Rubber Latex, Rubber Porous Structure, Rubber Drying Kinetics and Energy Consumption
DOI:
https://doi.org/10.37934/araset.29.2.159184Keywords:
Natural rubber, EMC isotherms, Drying kinetics, Energy consumption, RSS, STR20Abstract
Natural rubber (NR) is obtained principally from Para-rubber trees of the species Hevea brasiliensis which grow in tropical regions. Using ultra-centrifugation method, fresh latex (FL) from Para-rubber trees can be mainly divided into four fractions; an upper white layer consists of rubber particles, Frey-Wyssling particles in a yellow or an orange layer, C-serum phase and lutiods particles in the bottom fraction [1-3]. The averages of rubber particles have diameters of 0.02 to 3.0 micron, and they are protected by a complex film containing lipids and proteins [4-8]. The main forces of attraction between neighboring rubber particles in latex system can be divided into five force types; Structural Forces (SF), Van der Waals Interaction (VWI), Electrostatic Force (EF), Exclusion Interaction (EI) and Polymer-Polymer Interaction (PPI) [9]. The porous model of rubber structure used to describe moisture transfer was based on the existence of two different regions referred to as non-hygroscopic region and hygroscopic region. The rubber products drying always produced a considerable shrinkage effect which considered in the physical of the product, such as the diffusion coefficient, mass and heat transfer. An initial moisture content of raw material, the experimental temperature and the drying equipment had affect to the EMC isotherms and the drying kinetics. Finally, discussions on the implications of the results for strategies to reduce the energy consumption in RSS and STR20 block rubber are also presented.
Downloads
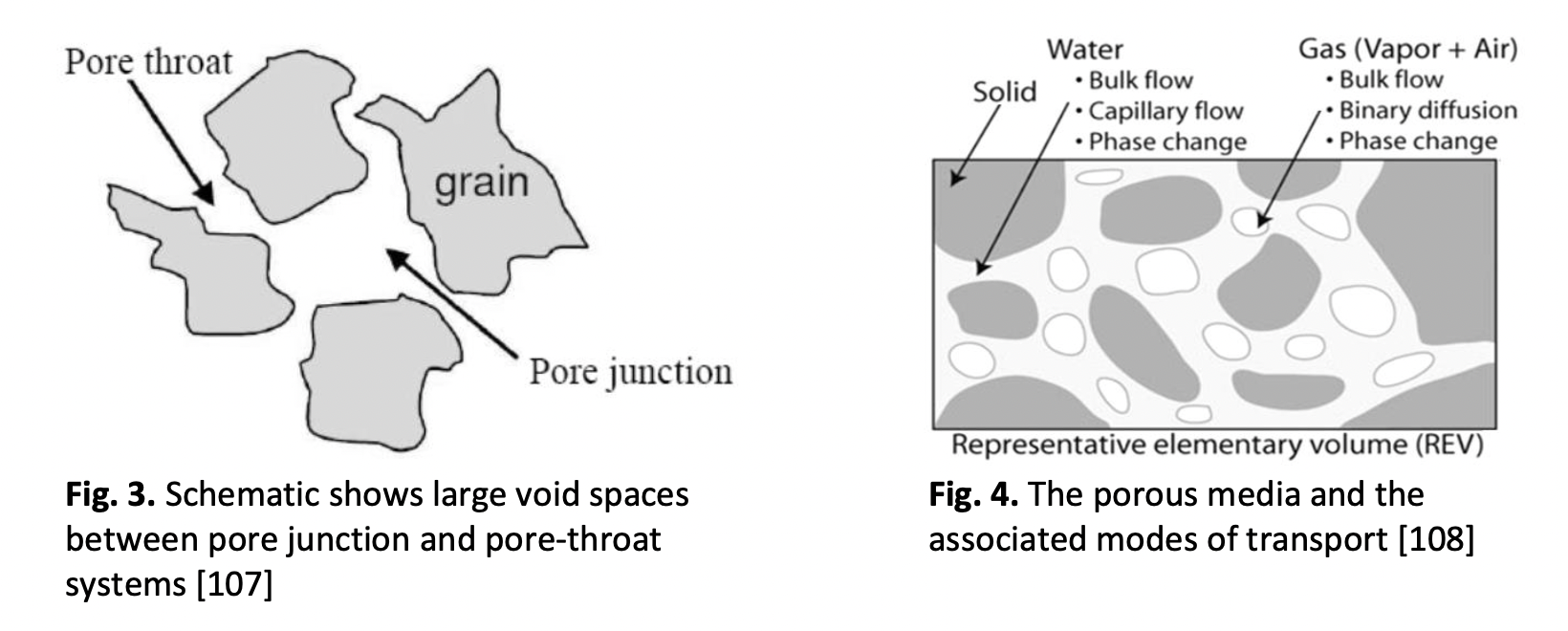