Effect of Buoyancy, Compressive Strength, and Shear Strength of Polyurethane-Clay Composite (PU-CC) Doped with Polyurethane Filler Waste in Soft Clay Application
DOI:
https://doi.org/10.37934/araset.31.3.106114Keywords:
PU filler, polyurethane waste, drying, subgrade layerAbstract
The application of polyurethane waste as a filler is one of the most cost-effective strategies for enhancing the geotechnical properties in soils. The PU waste from manufacturing economies was prepared with alkaline solutions by submerging into a 0.05 M sodium hydroxide (NaOH) before sieving to 300m sizes. The PU waste as filler was prepared using two heat exposure from microwaves and drying ovens at 60°C and left for 3 hours. Then, the treated and untreated Polyurethane-Clay Composite (PU-CC) was prepared at the different ratios of PU waste filler (2.5%, 5%, 7.5%, and 10%). The physical properties of treated and untreated Polyurethane-Clay Composite (PU-CC) were examined utilizing buoyancy force, unconfined compressive strength (UCS), and direct shear strength, respectively. The result exhibited that the PU-CCTO has the highest buoyancy force at 10% of PU-CCTO10 samples at 50%, followed by 45% of PU-CCTM10 and 8% of PU-CCUN2.5. The UCS and shear strength of PU-CCTO10 are evidently the highest at 300 kPa and 50 kPa, respectively, followed by PU-CCTM2.5 at 130 kPa and 19 kPa and PU-CCUN2.5 at 100 kPa and 15 kPa. PU-CCTO treated by drying oven has the highest buoyancy force at 10% of PU-CCTO10 samples at 50%, followed by 45% of PU-CCTM10 treated by microwave, and the lowest at 2.5 wt% of PU-CCUN2.5 untreated at 8%. In a nutshell, the prospective PU-CCTO is superior to the PU-CCUN and PU-CCTM related of the potential for overheating and burning the PU filler powder during the microwave processing procedure. In conclusion, the 10 wt% of PU filler treated by the drying oven method as a PU clay composite has the potential as an alternative material to improve the compressive strength, shear strength, and buoyancy force in soil improvement.
Downloads
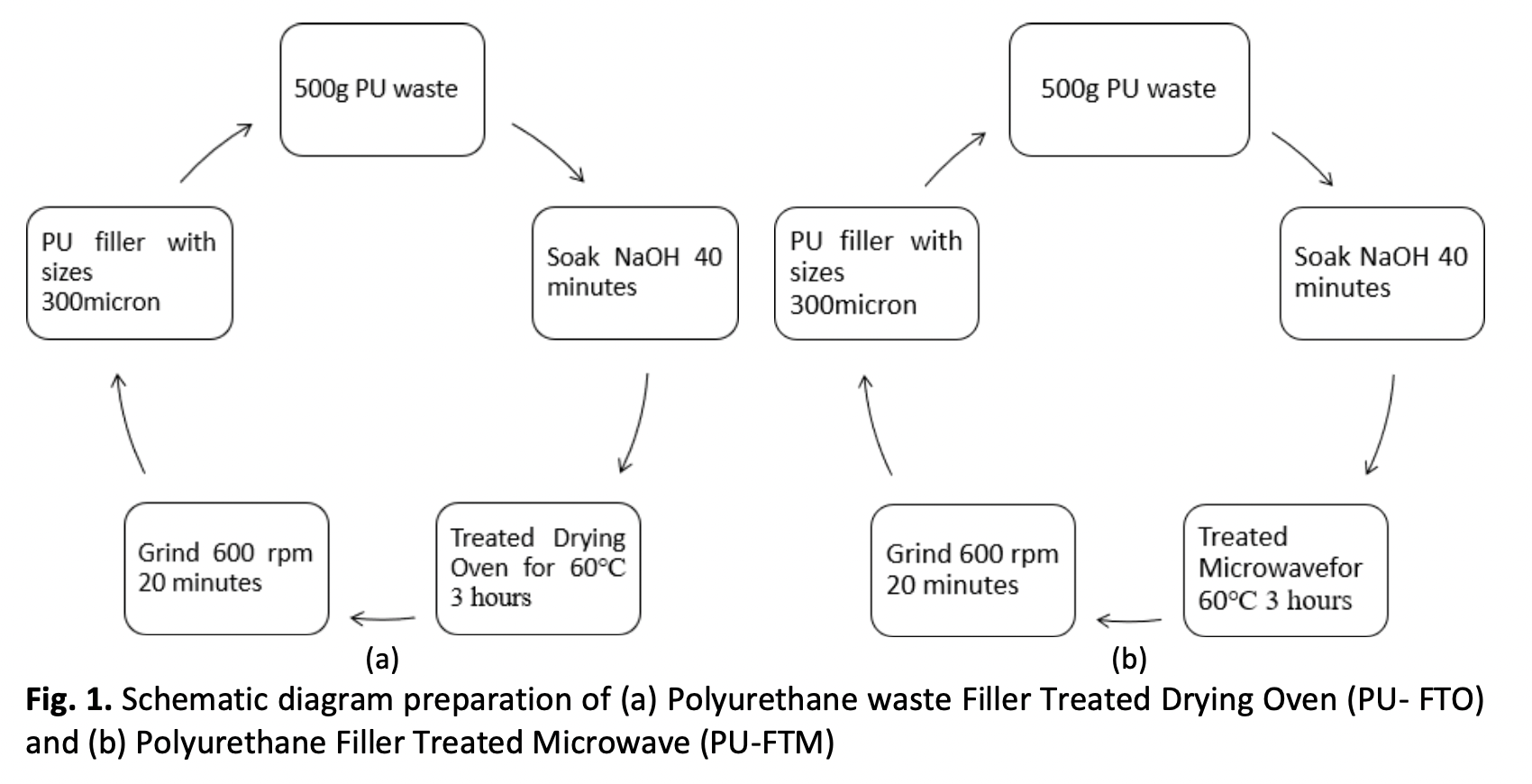