CFD Simulation of Aerodynamics Truck Using Cylinder as Drag Reduction Device
DOI:
https://doi.org/10.37934/arfmts.105.2.166181Keywords:
Truck, drag reduction, cylinder, CFD simulationAbstract
Reducing drag is an excellent approach to improving truck efficiency and saving fuel. The addition of the cylinder could be an alternative for drag reduction devices like the windshield that has a similar function to enhance the truck’s aerodynamic performance. A numerical analysis was performed using Ansys Fluent CFD software to estimate the influence of the cylinder on the truck's drag force. The study was conducted by comparing truck without additional cylinder above the truck’s head, truck with windshield, and truck with cylinder variations, which round, type-I, and type-D cylinders. In the simulation, the analysis was carried out at a velocity of 30 m/s using the k-epsilon turbulence model. A grid independence test was conducted to minimize errors and optimize iteration time. The simulation results showed that using round, I-type, and D-type cylinders as an alternative to the windshield reduced the truck's drag coefficient, with the D-type cylinder achieving the highest reduction in drag coefficient, which is 0.72. Modifications in the design of the drag reduction cylinder can lower fuel consumption indirectly by 6.95 % using a D-type cylinder.
Downloads
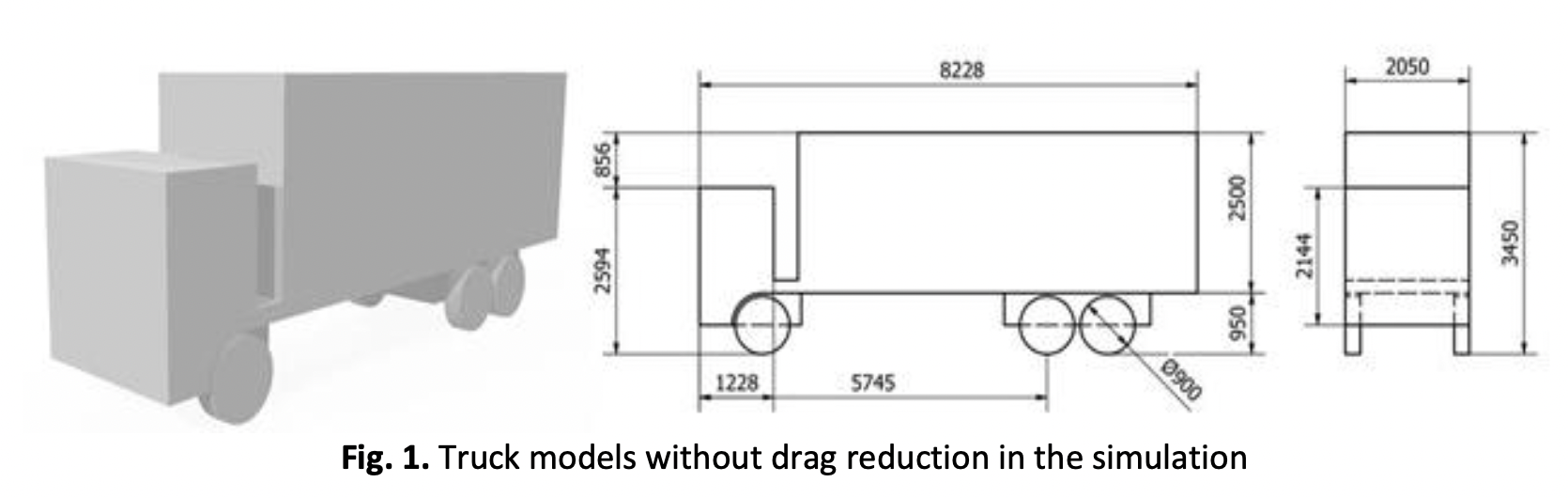