An Experimental Investigation on Melt Flow Index and Water Absorption of rHIPS/ABS/Kenaf Composite
DOI:
https://doi.org/10.37934/arfmts.108.1.103113Keywords:
Water absorption, melt flow index, composite, rHIPS, ABS, kenaf, SEBSAbstract
Despite increased awareness of environmental contamination, the recycling and modification of discarded plastics has gained popularity. In this study the composites of kenaf fibres incorporated in recycled high impact polystyrene (rHIPS)/acrylonitrile-butadiene-styrene (ABS) matrix with polypropylene-graft-maleic anhydride (MAPP) composites were mixed using twin screw extruder. This paper aims to examine the influence of water absorption and MFI of the composites. Ternary blends were prepared by varying the kenaf, MAPP loading from 0-30 (wt. %), at the varying conditions of ABS-rHIPS blends. For water absorption, the maximum percentage was 38.86% for 30 wt.% kenaf. It was noted that, rHIPS/ABS/kenaf composites which contains higher kenaf content showed greater water absorption due to higher fibre content and void percentages compared to composites having lesser amount of kenaf loading. The results also showed that the best MFI was from a mixture of 25% rHIPS, 65% ABS, 5% MAPP and 5% kenaf. From this mixture, the highest flow was produced and suitable for use in the production of products by using machines such as injection molding and extrusion. Due to the benefits associated with kenaf fibre composite as natural fibre, it can, therefore, be used as polymer reinforcement.
Downloads
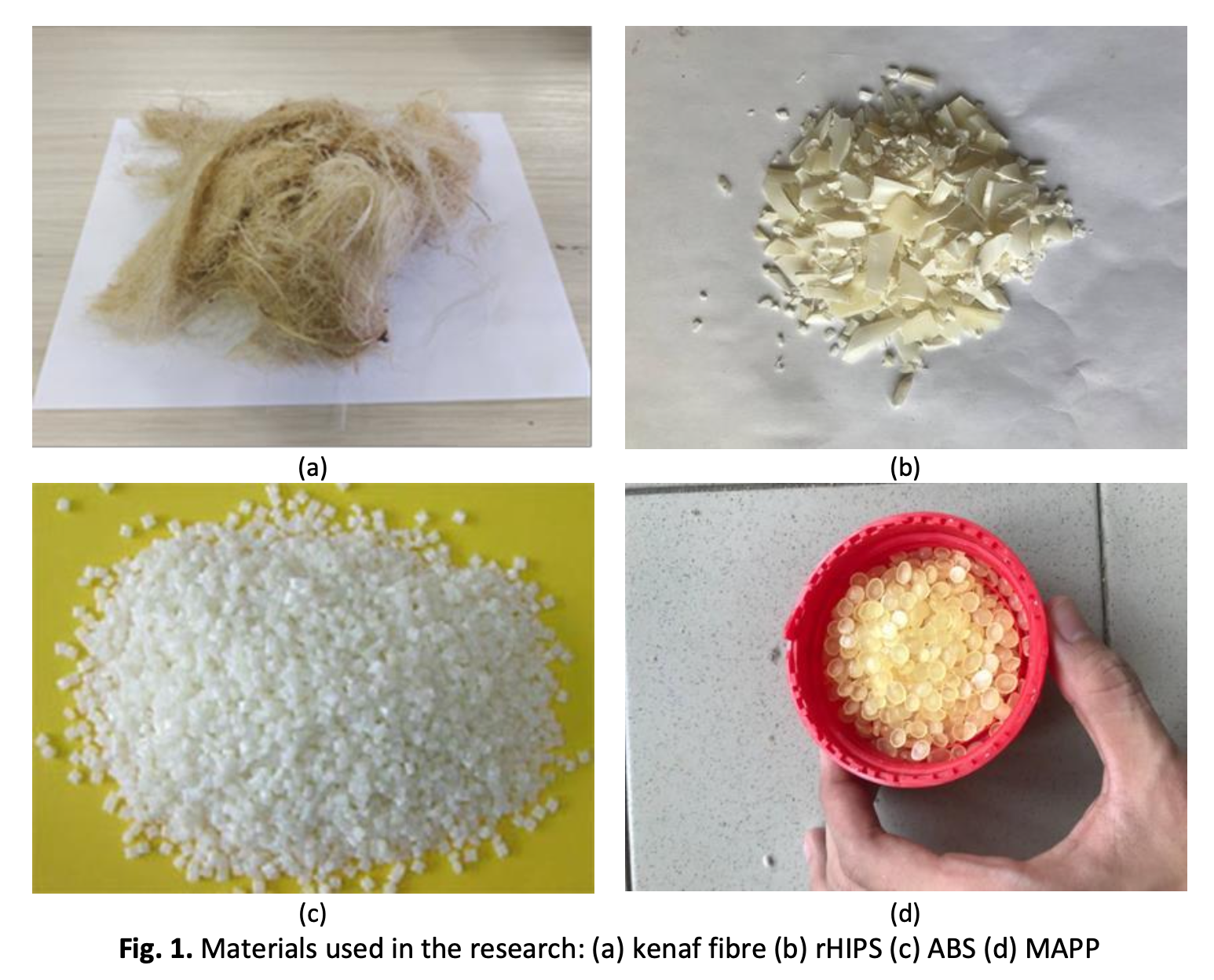