Numerical Investigation of Drag Force on Micro-sized Magnetic Beads in Microchannel with Chamber Design
Keywords:
Drag force, micro-sized bead, flow rate, microchannel, trapping chamber, microfluidicsAbstract
Biological cells or bioparticles separation is a primary step in most biological studies. One of the microfluidic bioparticles separation methods is the magnetic-based method. Integrated microfluidic magnetic bioparticle separation device is made up of a microfluidicschannel and a magnetic system. From past studies, the design of the microfluidic channel is least discussed in comparison with the magnetic system. To fill this gap, this study has focused on numerical simulation of a microfluidic channel with chamber design and the drag forces experienced by the magnetic beads. Simulation of the microfluidics channelwas donewithANSYS Fluent software. The width ratios of trapping chamber and main channel ranged from 1 to 20, the flow rates ranged from 1 μL/min to 100 μL/min, and the bead sizes ranged from 5 μm to 25 μmwere used in the numerical investigation. It was discovered that as the width ratio between the trapping chamber and main channel increases, the maximum velocity decreases, causing the Reynold’s number to decrease. The pressure drop becomegreater athigher flow rate. Higher width ratio causedthe drag force to reduceat a constant microbead size. At a constant width ratio between the trapping chamber and main channel, larger microbead sizes caused larger drag force. The microfluidic system with width ratio of 20 and flow rate of 1 μL/min produced the lowest drag force, 3.64 x 104pN. Since particle trapping would occur when the magnetic force is larger than the drag force, therefore ahigh gradient magnetic system which offered high magnetic force was proposedto be integrated with the microfluidics system.
Downloads
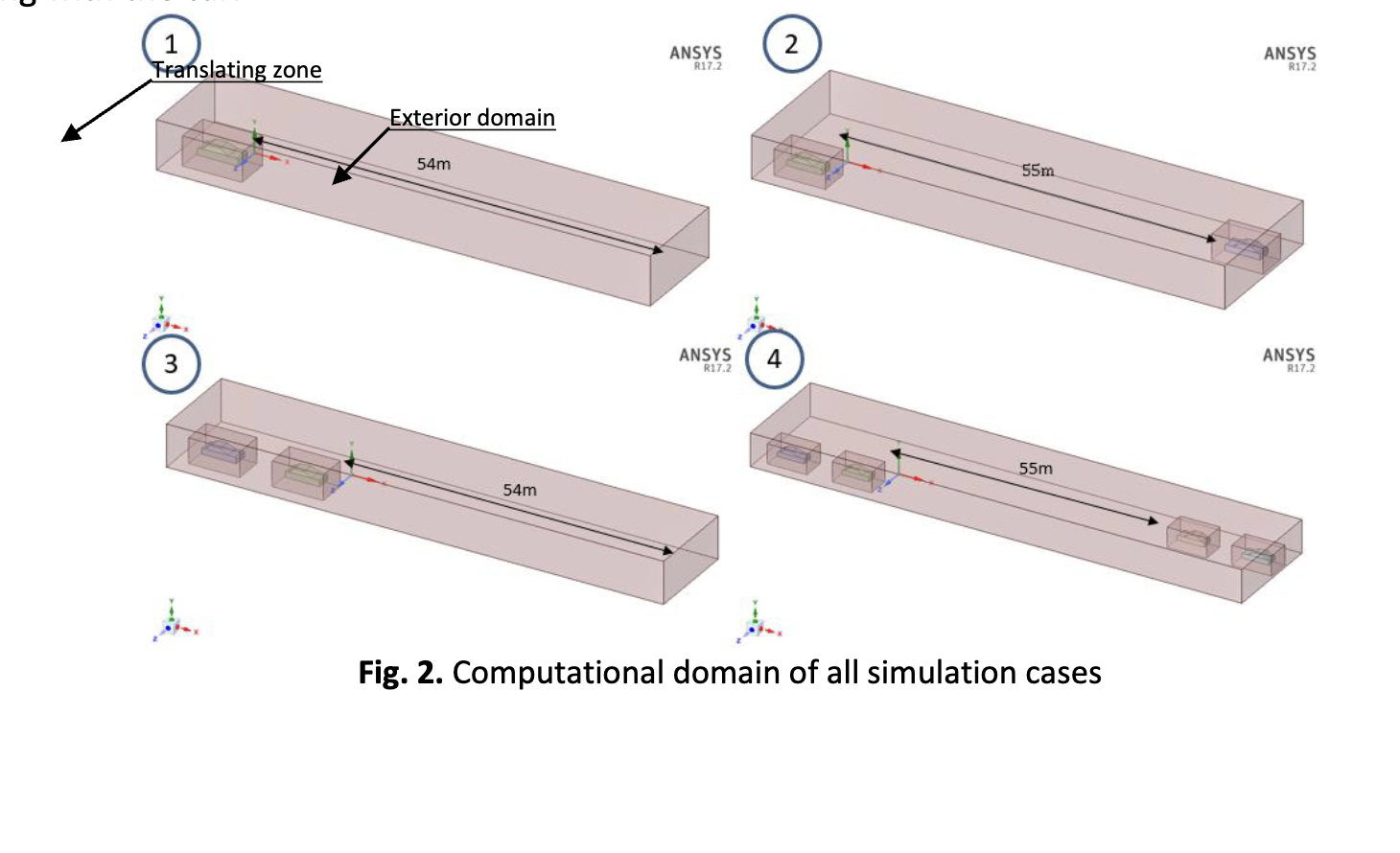