Aerodynamic Performance Investigation of a Small Horizontal Axis Wind Turbine with Multi-Airfoil Blade Profiles of SD2030 and E231 Using Wind Tunnel Experiments and BEM Theory Method
DOI:
https://doi.org/10.37934/arfmts.103.1.150164Keywords:
Low Reynolds number airfoil, small multi-airfoil turbine blade, wind tunnel test, low start up speed, tip speed ratio, power coefficient, QBlade, energyAbstract
The goal of this study is to investigate the performance of a small horizontal axis wind turbine blade at wind speeds of lower than 5 m/sec numerically and experimentally. The rotor blade has a diameter of 0.7m and consists of two airfoils profile: the thin airfoil SD2030 selected at the outboard region, and the thick airfoil E231 at the inboard region. The former airfoil, SD2030, is highly recognized for aerodynamic performance as it is suitable for low Reynolds number (Re), while the latter airfoil E231 is likewise appropriate for low Re flow but has a higher thickness-to-chord ratio which acts as structural support and good strength at the hub. The selected airfoils were analyzed using QBlade software based on XFOIL and Blade Element Theory (BEM) for different Reynolds number. Using a low-speed wind tunnel and Reynolds number ranging from 1x105 to 5x105, experiments at pitch angles of 5ο were conducted to determine the variation in torque and predict blade performance. The results reveal that the turbine with two hybrid different airfoil profiles have achieved a better start-up response at low wind speed of 1.5 m/s and a high-power coefficient of 0.34 with 3.7 tip speed ratio. The turbine can be used to generate a power of 0.5W at 1.5 m/s and a maximum power harvest of up to 20W at a wind speed of 7m/sec. The turbine's performance compared to other small wind turbines from the literatures demonstrate good performance and the results obtained from wind tunnel data were found in satisfactory agreement with the results provided by the BEM code.
Downloads
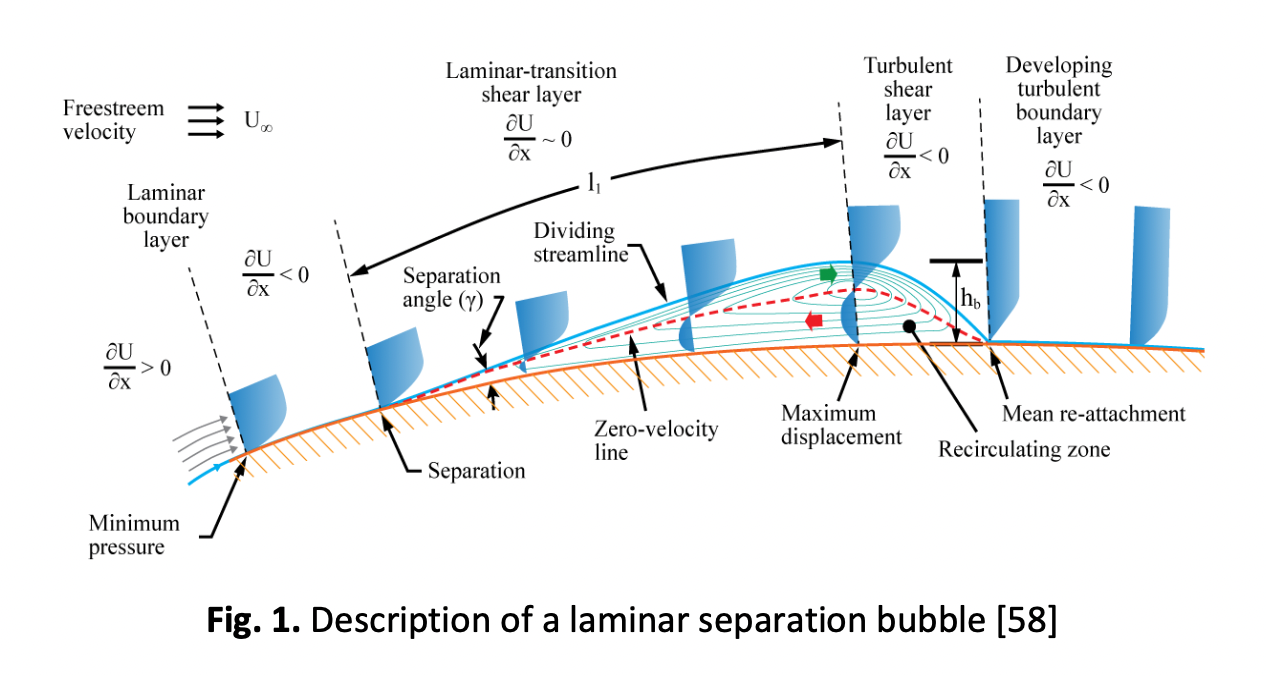