Thermo-Hydraulic Performance of Heated Tube with Twisted Delta Winglet Swirler Insert: A Numerical Simulation
DOI:
https://doi.org/10.37934/arfmts.100.1.181200Keywords:
Convective heat transfer enhancement, friction factor, thermal-hydraulic performance, swirler, turbulatorAbstract
Among the various methods for enhancing heat transfer in a heat exchanger, a passive method of inserting a continuous swirler inside a heated tube provides a secondary flow along the fluid that reduces the thickness of the thermal boundary layer, thus increasing the efficiency of convection heat transfer performance. The research’s primary goal is to conserve energy, materials, and money by operating efficient heat exchanger equipment. However, the continuous swirler along the fluid flow creates a persistent obstruction, which amplifies the friction factor and increases the working fluid’s energy loss. As a result, this research presented the twisted delta winglet swirler (TDWS), a new design of a decaying swirler that uses delta winglets twisted to 180° to produce a swirling flow along the tube. The swirler comprises four twisted delta winglets arranged in a circle with a diameter 6% smaller than the tube and a length of L/D=2.2. It was placed at the entrance to a heated tube test section with a diameter of 0.016 m and a length of L/D=93.75. The Reynolds Stress Model was used to simulate the flow domain with a water-ethylene glycol mixture was chosen as the working fluid. TDWS transformed the uniform inlet flow from potential energy to high kinetic energy, resulting in a high intensity of swirling flow downstream of the circular tube up to L/D=46.88 before decaying and reaching a steady state. Compared to other decaying swirlers, TDWS obtained one of the lowest relative friction factors, 1.36, with this flow. The maximum global relative Nusselt number increased by only 11% because this value considered the area where the flow reached a steady state. Since the TDWS is a decaying swirler, the thermal-hydraulic performance reached unity along the tube. However, the optimal performance of TDWS in the plain tube with a length of L/D=93.75 can be found if the dimension or geometric configuration of the TDWS is modified, or two or more TDWS may be placed in an array orientation.
Downloads
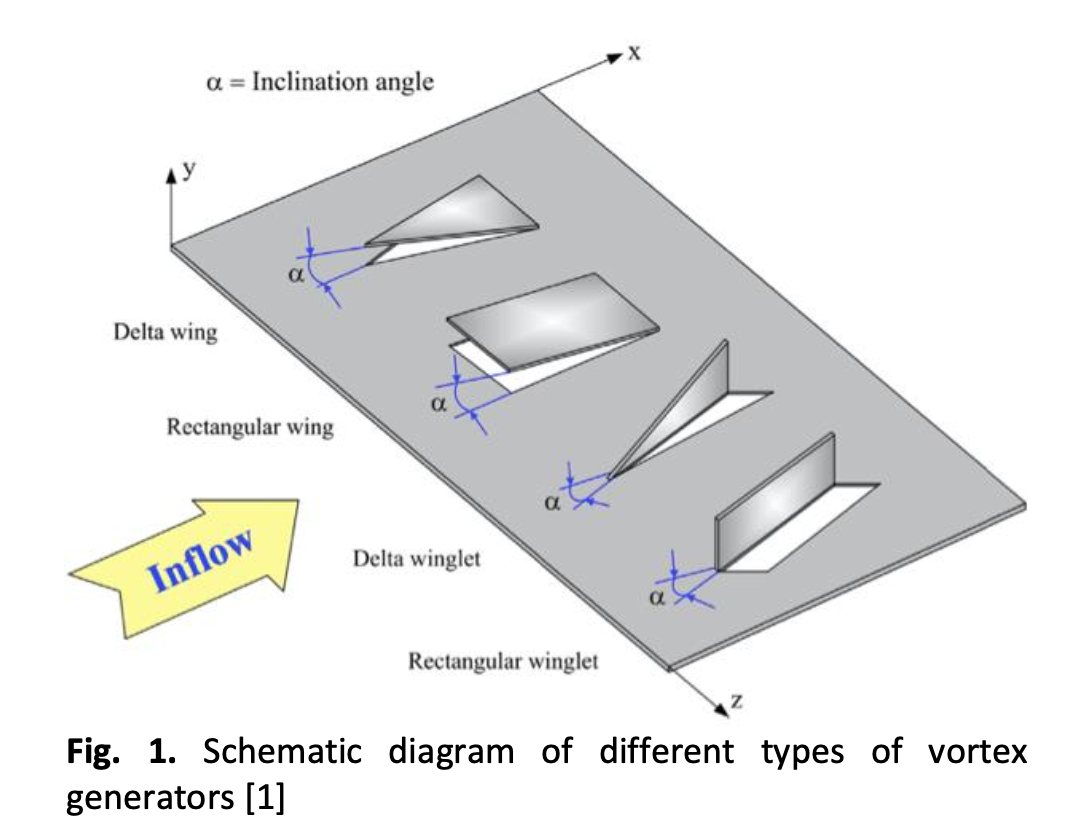