Numerical Simulation of Aerofoil with Flow Injection at the Upper Surface
Keywords:
CFD, Flow Injection, Airfoil, NACA0012Abstract
Separation of the boundary layer over an airfoil causes a significant increase in the
adverse pressure gradients and the losses of energy resulting in the reduction of the
lift force and the increment of drag force. Therefore, delaying and eliminating flow
separation is necessary to improve its aerodynamic characteristics. In this study, an
injection of flow was introduced at the upper surface/suction side of the aerofoil to
control the boundary layer separation effectively. Flow around the NACA0012 airfoil
was examined, with the position of flow injection jet at 90° relative to the tangential
surface of the airfoil at 20%, 50% and 80% of its chord length. The flow injection
velocity was varied from 0%, 10%, 30% and 50% of the free stream velocity, which
corresponds to 0, 2.5 x 10-4, 2.25 x 10-3 and 6.25 x 10-3 of the momentum coefficient.
The results showed that the most suitable condition was at 10% of the blowing
amplitude (2.5 x 10-4 of the momentum coefficient) of flow injection at the trailing
edge, which was around 80% of the chord length at the upper surface/suction side.
This configuration can successfully increase the lift force and decrease the drag force
of the aerofoil at the angle equal to or larger than a stall angle of 16° compared to the
baseline aerofoil.
Downloads
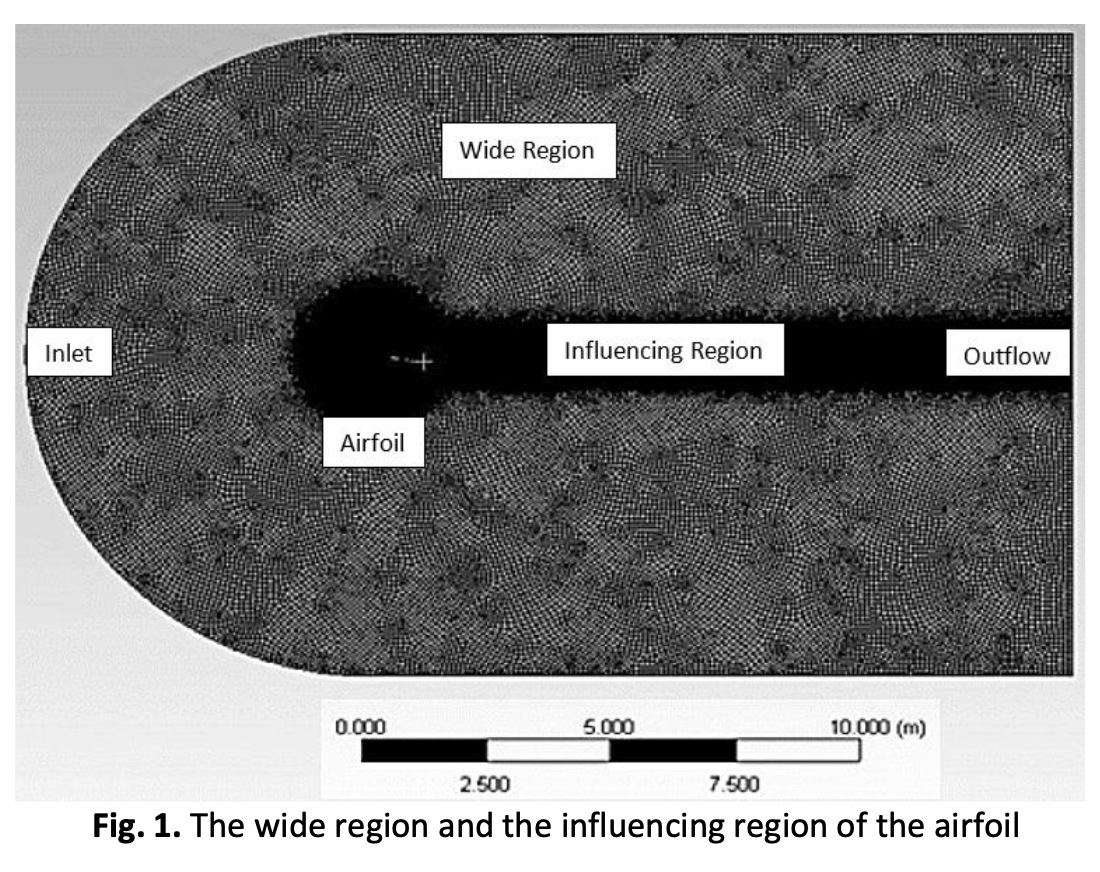