Twist Blade Distributor in Fluidization Systems: Part 1 – The Computational Procedure
DOI:
https://doi.org/10.37934/araset.29.2.111Keywords:
Fluidized bed, Twist blade distributor, Velocity magnitude, Tangential velocityAbstract
Flowing gas in fluidized bed through selected inlet distributor may imparts a drag effect on the particles, would cause an increase in gas flow, that maybe sufficient to rearrange the particles movement. Thus, study on the airflow in a fluidization system through numerical analysis has been conducted to investigate the airflow distribution affected by new model distributor of twist blade distributor configuration. The present study would emphasis on computational procedure and parametric study via ANSYS Fluent before a detailed study on selected twist blade distributor are conducted. The selected parametric study on the twist blade distributor configuration whereby the twist blade angle (100°), horizontal inclination angle (15°), radial inclination angle (10°) and number of blades (60) was carried out. Therefore, the results of the studies that have been carried out meet the expected standards based on previous studies.
Downloads
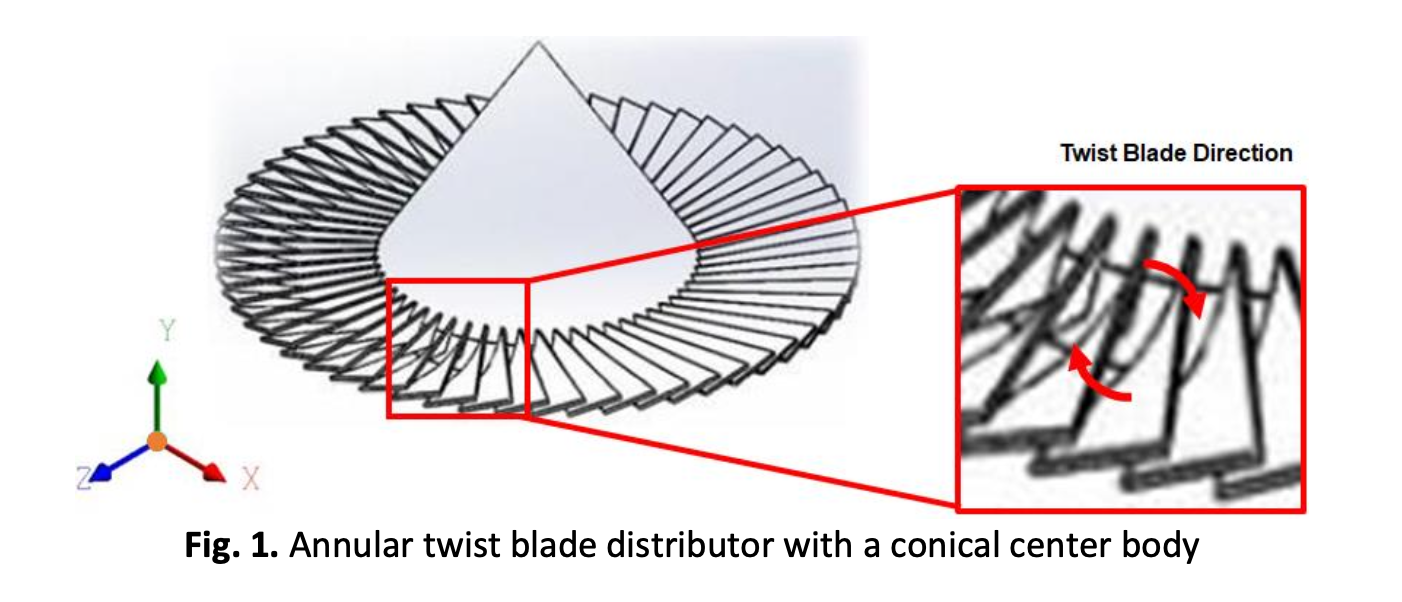