High Densification Level and Hardness Values of Additively Manufactured 316L Stainless Steel Fabricated by Fused Filament Fabrication
DOI:
https://doi.org/10.37934/araset.34.2.144152Keywords:
Additive manufacturing, fused filament fabrication, 316L stainless steel, densification level, hardnessAbstract
Laser powder bed fusion (L-PBF) has emerged as the most widely used additive manufacturing (AM) process, also known as 3D printing, to fabricate 316L stainless steel (316L SS) components for various applications. However, the initial setup, operation, and maintenance costs are too expensive due to the complex machinery, high energy-consuming laser beam, and proprietary software required. Therefore, in this paper, fused fiament fabrication (FFF) is proposed as a low-cost AM approach to fabricate 316L SS specimens via a 3-step printing-debinding-and sintering process. The specimens are initially printed on a desktop FFF AM 3D printer by varying nozzle temperatures from 195 – 220°C, followed by debinding up to 427°C for 4 hours, and finally sintering at 1260°C for 4 hours. The results show that nozzle temperature 200°C yielded the highest densification level of 97.6% and highest average hardness value of 292 HV, indicating that 3D printing parameters, particularly nozzle temperature plays an important role in influencing the properties of the sintered specimens. Overall, the results from this study prove that FFF is a viable and cost-effective AM process that has the potential to produce 316L SS parts that meet industrial requirements.
Downloads
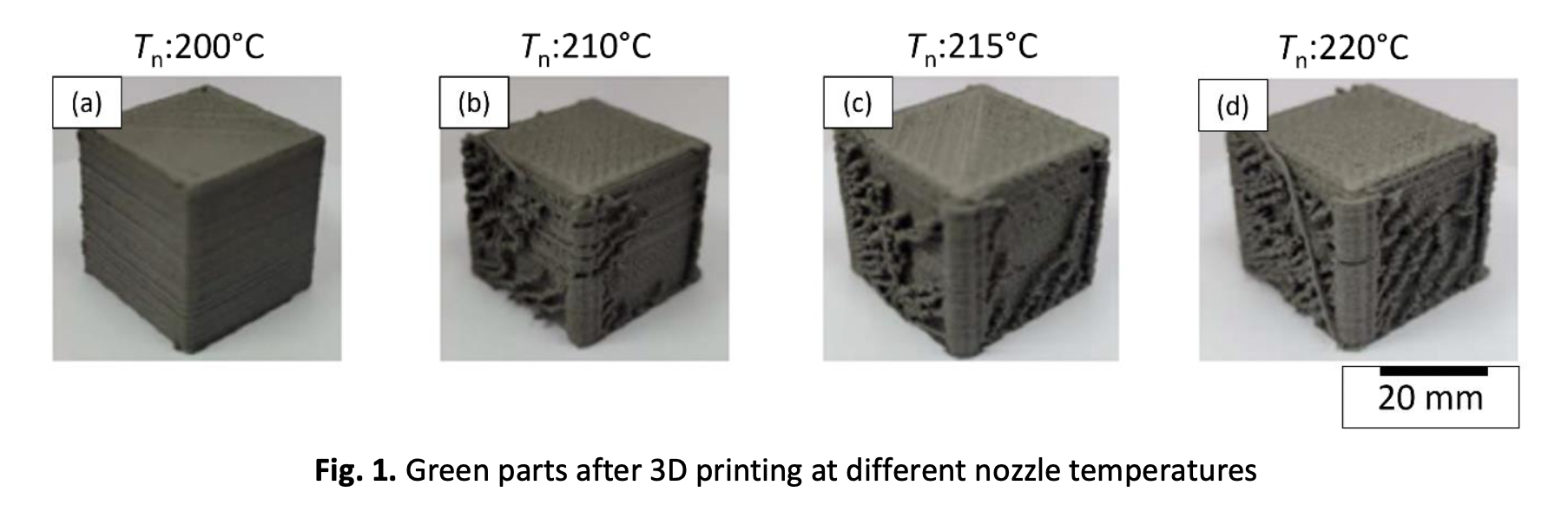