Design and Implementation of Hybrid Exoskeleton for Oil Palm Harvester to Reduce Muscle Strain
DOI:
https://doi.org/10.37934/aram.105.1.111Keywords:
EMG signal, Gravitational compensation, Hybrid exoskeleton, Iso-elasticity, work-elated musculoskeletal disorders (WMSD)Abstract
When it comes to safety at the workplace, palm oil harvesters are highly exposed to body pain and muscular fatigue, which in the long term may lead to permanent spinal or shoulder damage that will undoubtedly result in different extreme societal difficulties. Meager investment in safety and long hours of manual work in awkward posture is the main challenge in ensuring safety in the palm oil field. This study aimed to develop a novel light hybrid exoskeleton exclusively built for palm oil harvesting to reduce muscular strain, maintain minimum cost, and ensure material availability in the local market. The iso-elasticity approach and DC linear motor were used for gravitational and muscular torque compensation and position control. Muscular EMG signal was taken and filtered to investigate the muscle strain reduction after implementing the developed hybrid exoskeleton. The result shows that the overall muscle strain was reduced by 16% using the passive exoskeleton and 23% using the hybrid exoskeleton compared to freehand. According to the results, it is evident that the developed exoskeleton can be implemented in palm oil harvesting, which will reduce the pain level of the workers at a significant rate.
Downloads
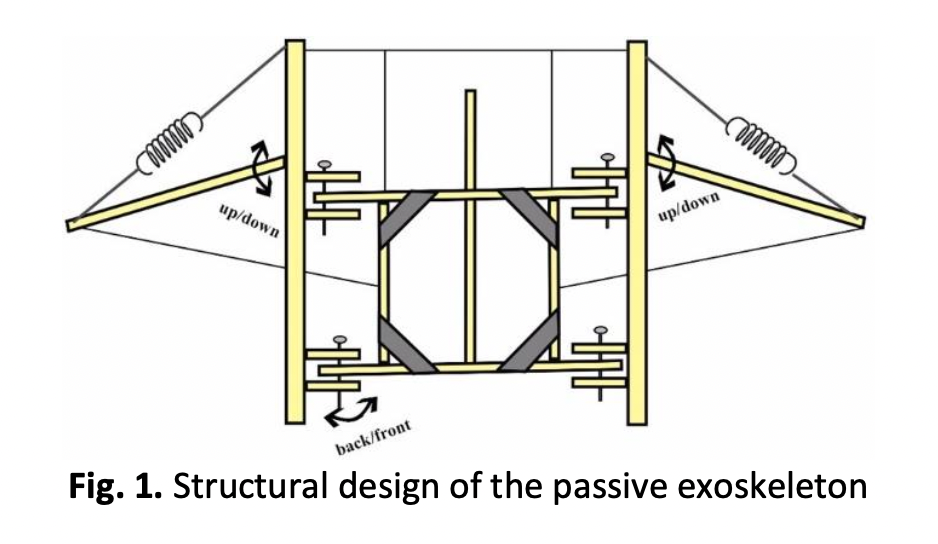