CFD Impingement Flow Study on Temperature Profile of Concave Plate
DOI:
https://doi.org/10.37934/arfmts.95.1.116Keywords:
CFD, anti-icing, temperatureAbstract
All the aircraft are equipped with an anti-icing system to prevent ice accretion on the body of the aircraft. The anti-icing system is important because ice accretion degrades the performance of the aircraft and may cause aircraft crashes. Piccolo tube Anti-icing system uses the impingement hot air and creates hotspot on nacelle lip-skin and edges of wings. The temperature distribution caused by the impingement of hot air must be studied to get a better design of the anti-icing system. The skin geometry shape affects hot airflow behavior in the impingement vicinity, hence influences temperature distribution on wing skin and nacelle lip-skin. Thus, the CFD simulation of the hot air impingement air various concave curvature radius was conducted by using ANSYS Fluent 19.2. The result shows the temperature contour has been plotted from the software. Correlation between Nusselt number on impingement point and Reynolds number was successfully done as the validation. Increasing the Reynolds number increases the dimensionless temperature of the concave plate. Temperature is 0.147125 has been recorded as the highest dimensionless temperature under the set of an air temperature of 43°C, Reynolds number of 4070, and 300mm curvature radius. Besides that, increases in heat dissipation decrease the dimensionless temperature of the plate with the curvature radius also decreases. The dimensionless temperature increases from 0.138747 to 0.142316 when the curvature radius increases from 150mm to 300mm.
Downloads
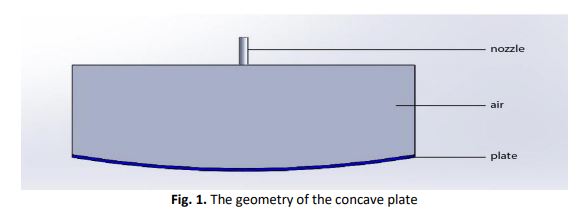